Stevens Croft: Difference between revisions
No edit summary |
No edit summary |
||
(11 intermediate revisions by 3 users not shown) | |||
Line 1: | Line 1: | ||
A [[Biomass EfW]] facility [[Stevens Croft]] is a [[CHP]] plant based on processing up to 480,000 tonnes per annum of [[Wood Waste]] and [[Biomass]]<ref name="SC">[https://www.mottmac.com/article/2282/stevens-croft-biomass-power-station-uk/ Mott MacDonald]</ref>. | |||
[[Category:Biomass EfW Plants]]{{#vardefine: epr|tbc5}} | |||
{{BiomassPlant|NAME=Stevens Croft|id=76|EPR={{#var: epr}}}} | |||
[[File:EON-Stevens-Croft.jpg|300px|left|Steven's Croft Biomass Facility]]__TOC__ | |||
<br clear="left"/> | |||
==Summary== | ==Summary== | ||
A Biomass | A [[Biomass EfW]] facility [[Stevens Croft]] is a [[CHP]] plant based on processing up to 480,000 tonnes per annum of [[Wood Waste]] and [[Biomass]]<ref name="SC" />. The plant was developed and is owned by [[E.ON UK]] and cost an estimated €132m<ref name="tech">[https://www.power-technology.com/projects/stevenscroftbiomass/ Power Technology]</ref>. | ||
Steven's Croft in Lockerbie Scotland, | Steven's Croft is located in Lockerbie Scotland, has an output of 44 MWe to the grid and 6.5 MWth, the facility supplies c. 70,000 homes, displacing 140,000 tonnes of greenhouse gases<ref name="SC" />. | ||
The | Construction of the facility at Steven's Croft not only included the biomass plant but a fuel processing facility and 26km of underground electrical cable connecting the plant to Chapel Cross electrical sub-station<ref name="SC" />. The fuel processing facility was designed to blend all the various sources of fuel mentioned above into one homogeneous material. It includes up to 14 days of round wood storage, a facility for reception of pre-chipped fuel, up to 6000m3 of covered chipped fuel storage, a round wood chipping facility, fuel reclamation and forwarding equipment with systems for final preparation of the fuel before delivery to the power plant.<ref name="SC" /> | ||
The facility also provides electricity to its fuel provider [[AW Jenkinsons]] and supplies heat to the neighbouring sawmill, [[James Jones and Sons]]<ref>[https://www.eonenergy.com/About-eon/our-company/generation/our-current-portfolio/biomass/stevens-croft/ E.ON]</ref>. | |||
==Plant== | ==Plant== | ||
Construction of the plant began in October 2005 with the plant entering commissioning in Autumn 2007 <ref name="tech" />. Construction was carried out by a Siemens/Kvaerner consortium with the boiler being a Kvaerner Power Bubbling Fluidised Bed power boiler, fuel handling and flue gas cleaning equipment<ref name="tech" />. The boiler conditions were designed to allow the best efficiency at 537°C, 137Bar with a capacity to raise 16 MWth of energy. The high steam conditions dictate the need for specialist corrosion resistant materials in the high temperature components and to control fuel quality.<ref name="SC" /> | Construction of the plant began in October 2005 with the plant entering commissioning in Autumn 2007 <ref name="tech" />. Construction was carried out by a [[Siemens]]/[[Kvaerner]] consortium with the boiler being a [[Kvaerner Power Bubbling Fluidised Bed]] power boiler, fuel handling and flue gas cleaning equipment<ref name="tech" />. The boiler conditions were designed to allow the best efficiency at 537°C, 137Bar with a capacity to raise 16 MWth of energy. The high steam conditions dictate the need for specialist corrosion resistant materials in the high temperature components and to control fuel quality.<ref name="SC" /> | ||
Siemens provided overall coordination, engineering and project management as well as the civil works and electrical and I&C equipment<ref name="tech" />. | [[Siemens]] provided overall coordination, engineering and project management as well as the civil works and electrical and I&C equipment<ref name="tech" />. | ||
The power plant can reach full output | The power plant can reach full output with high moisture fuels. It is able to burn a maximum of 20% recycled wood (limited by Planning and its [[The Pollution Prevention and Control (Scotland) Regulations 2012|IPPC Permit]]) and a maximum of 20% short rotation coppice. [[Moisture Content]] for the plant is between 46% and 58%, with a design blend of 53%<ref name="tech" />. | ||
{{BioSustain|EPR={{#var: epr}}}} | |||
{{EAIn|EPR={{#var: epr}}}} | |||
The feedstock for the plant can include forest wood and agricultural residues, urban wastes and energy crops, and the feedstock split on the website is shown as comprising<ref name="SC" />: | |||
*60% sawmill co-products and small roundwood | |||
*20% short rotation coppice (willow) | |||
*20% recycled fibre from wood product manufacture. | |||
although the [[Annual Sustainability Report]] does not breakdown the mixture of virgin wood types into their component types. | |||
==References== | ==References== |
Latest revision as of 09:03, 15 August 2022
A Biomass EfW facility Stevens Croft is a CHP plant based on processing up to 480,000 tonnes per annum of Wood Waste and Biomass[1].
Stevens Croft Operational | |
![]() See Biomass EfW → page for a larger UK Wide map. | |
Operator | E-On |
Capacity | 44 MWe |
Feedstock | Waste Wood/Virgin |
EPR (Waste Licence) | PPC/A/1011415 |
ROC | Yes |
CfD | |
CHP | Yes |
Operators Annual Report
Input Data
Year | Wood | Litter | RDF | Other | Total |
---|
Output Data
Year | IBA | IBA %ge of Tot IN | APC | APC %ge of Tot IN |
---|
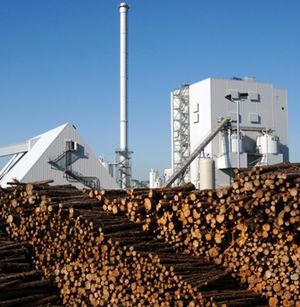
Summary
A Biomass EfW facility Stevens Croft is a CHP plant based on processing up to 480,000 tonnes per annum of Wood Waste and Biomass[1]. The plant was developed and is owned by E.ON UK and cost an estimated €132m[2].
Steven's Croft is located in Lockerbie Scotland, has an output of 44 MWe to the grid and 6.5 MWth, the facility supplies c. 70,000 homes, displacing 140,000 tonnes of greenhouse gases[1].
Construction of the facility at Steven's Croft not only included the biomass plant but a fuel processing facility and 26km of underground electrical cable connecting the plant to Chapel Cross electrical sub-station[1]. The fuel processing facility was designed to blend all the various sources of fuel mentioned above into one homogeneous material. It includes up to 14 days of round wood storage, a facility for reception of pre-chipped fuel, up to 6000m3 of covered chipped fuel storage, a round wood chipping facility, fuel reclamation and forwarding equipment with systems for final preparation of the fuel before delivery to the power plant.[1]
The facility also provides electricity to its fuel provider AW Jenkinsons and supplies heat to the neighbouring sawmill, James Jones and Sons[3].
Plant
Construction of the plant began in October 2005 with the plant entering commissioning in Autumn 2007 [2]. Construction was carried out by a Siemens/Kvaerner consortium with the boiler being a Kvaerner Power Bubbling Fluidised Bed power boiler, fuel handling and flue gas cleaning equipment[2]. The boiler conditions were designed to allow the best efficiency at 537°C, 137Bar with a capacity to raise 16 MWth of energy. The high steam conditions dictate the need for specialist corrosion resistant materials in the high temperature components and to control fuel quality.[1]
Siemens provided overall coordination, engineering and project management as well as the civil works and electrical and I&C equipment[2].
The power plant can reach full output with high moisture fuels. It is able to burn a maximum of 20% recycled wood (limited by Planning and its IPPC Permit) and a maximum of 20% short rotation coppice. Moisture Content for the plant is between 46% and 58%, with a design blend of 53%[2].
Annual Sustainability Tonnage Input/Fuel
The tonnage[4] received by the plant in the most recent Annual Sustainability Report and for the previous 3 years for Error: no local variable "asyear" has been set. was reported by Ofgem as below[5]:
Year | Waste Wood (m3) | Waste Wood (t) | Straw | Miscanthus | Arboricultrual Waste | Sawmill Residue | Foresrty Residue | Round Wood | Short Rotation Coppice | MBM | Other Material |
---|
Waste Tonnage, By Origin
The table shows a list of the Waste for the Permit tbc5, that has arrived into sites as reported to the Regulator and then publicised in their reported statistics. The Data used is from the most recent returns. The total reported tonnage arriving at the site was: Expression error: Unexpected < operator.t.
Where this tonnage exceeds that reported in year of the corresponding annual report, this may be due to the following reasons:
- Tonnage may have been received but not incinerated, i.e. the material is held pending incineration (the operator return to the EA reports as received whereas the annual report focuses on when the waste is incinerated.)
- Material may have been received into the site but treated in some other way than incineration.
- Material may have been received on the but transferred out of site for disposal/treatment at another site rather than incineration on the site.
EWC Code | Origin of Waste | Tonnes In |
---|
The feedstock for the plant can include forest wood and agricultural residues, urban wastes and energy crops, and the feedstock split on the website is shown as comprising[1]:
- 60% sawmill co-products and small roundwood
- 20% short rotation coppice (willow)
- 20% recycled fibre from wood product manufacture.
although the Annual Sustainability Report does not breakdown the mixture of virgin wood types into their component types.
References
- ↑ Jump up to: 1.0 1.1 1.2 1.3 1.4 1.5 1.6 Mott MacDonald
- ↑ Jump up to: 2.0 2.1 2.2 2.3 2.4 Power Technology
- ↑ E.ON
- ↑ In the case of EfW plants with gasification technology the figures are reported in terms of cubic metres of syngas produced rather than tonnes used
- ↑ Biomass Sustainability Dataset 2020-21