Pyrolysis: Difference between revisions
No edit summary |
mNo edit summary |
||
Line 1: | Line 1: | ||
[[Category:Technologies & Solutions]] | [[Category:Technologies & Solutions]] | ||
[[Pyrolysis]] is the thermal degradation of waste in the absence of oxygen to produce gas ([[Syngas|syngas]]), liquid and solid char fractions. The [[Syngas|syngas]] is then generally burnt to raise steam and create electricity, but many plants are exploring the option of cleaning the [[Syngas|syngas]] for use in a gas engine or separating the gas into usable fractions such as hydrogen for use, as an example, of liquid fuels which in turn may be eligible under the [[RTFO]]. The solid residue (sometimes described as a char) is a combination of non-combustible materials and carbon. | [[Pyrolysis]] is the thermal degradation of waste in the absence of oxygen to produce gas ([[Syngas|syngas]]), liquid and solid char fractions. The [[Syngas|syngas]] is then generally burnt to raise steam and create electricity, but many plants are exploring the option of cleaning the [[Syngas|syngas]] for use in a gas engine or separating the gas into usable fractions such as hydrogen for use, as an example, of liquid fuels which in turn may be eligible under the [[RTFO]]. The solid residue (sometimes described as a char) is a combination of non-combustible materials and carbon. | ||
==Description== | |||
The process generally requires an external heat source to maintain the temperature required and to avoid the introduction of air. There are a range of different types of approach, often aligned to the waste being processed, and include fixed bed reactors, batch or semi-batch reactors, rotary kilns, fluidized bed reactors, microwave assisted reactors and some innovative solutions like plasma or solar reactors <ref> Czajczyńska et al, 2017. Potential of pyrolysis processes in the waste management sector. Thermal Science and Engineering Progress, [online] 3, pp.171-197. </ref>. | The process generally requires an external heat source to maintain the temperature required and to avoid the introduction of air. There are a range of different types of approach, often aligned to the waste being processed, and include fixed bed reactors, batch or semi-batch reactors, rotary kilns, fluidized bed reactors, microwave assisted reactors and some innovative solutions like plasma or solar reactors <ref> Czajczyńska et al, 2017. Potential of pyrolysis processes in the waste management sector. Thermal Science and Engineering Progress, [online] 3, pp.171-197. </ref>. | ||
[[File:The Biomass Pyrolysis-Cycle.png|600px|left|The Biomass Pyrolysis Cycle. All rights reserved.]] | |||
<br clear=all /> | |||
Typically, lower temperatures of between 300C to 850C are used during Pyrolysis of materials such as [[MSW]]. Pyrolysis processes tend to prefer consistent feedstocks and there is a limited track record of commercial scale Pyrolysis plant accepting [[MSW]] but a better track record of, for example, Pyrolysis of [[Biomass|biomass]] <ref> Defra, 2013. [https://assets.publishing.service.gov.uk/government/uploads/system/uploads/attachment_data/file/221035/pb13888-thermal-treatment-waste.pdf Advanced Thermal Treatment of Municipal Solid Waste.] London. </ref>. | Typically, lower temperatures of between 300C to 850C are used during Pyrolysis of materials such as [[MSW]]. Pyrolysis processes tend to prefer consistent feedstocks and there is a limited track record of commercial scale Pyrolysis plant accepting [[MSW]] but a better track record of, for example, Pyrolysis of [[Biomass|biomass]] <ref> Defra, 2013. [https://assets.publishing.service.gov.uk/government/uploads/system/uploads/attachment_data/file/221035/pb13888-thermal-treatment-waste.pdf Advanced Thermal Treatment of Municipal Solid Waste.] London. </ref>. | ||
==Types of Pyrolysis == | |||
The pyrolysis process can be divided into three subcategories depending on the operating conditions: temperature, heating rate, particle size and solid residence time. The different types of pyrolysis are slow/conventional, fast and flash. | The pyrolysis process can be divided into three subcategories depending on the operating conditions: temperature, heating rate, particle size and solid residence time. The different types of pyrolysis are slow/conventional, fast and flash. | ||
=== Slow/Conventional === | |||
Slow/conventional pyrolysis is a process where the heating rate is kept slow (around 0.1-1°C/s) which results in higher char yield than the liquid and gaseous products. This type of pyrolysis has been used for thousands of years for the production of charcoal. [[Biomass]] is heated to around 500°C in slow [[Wood|wood]] pyrolysis and the long vapour residence time in the reactor means the gas-phase products have ample opportunities to react with other products to form char<ref name="ref1">[http://www.eagri.org/eagri50/AENG352/lec10.pdf Principles of Pyrolysis]</ref>. | Slow/conventional pyrolysis is a process where the heating rate is kept slow (around 0.1-1°C/s) which results in higher char yield than the liquid and gaseous products. This type of pyrolysis has been used for thousands of years for the production of charcoal. [[Biomass]] is heated to around 500°C in slow [[Wood|wood]] pyrolysis and the long vapour residence time in the reactor means the gas-phase products have ample opportunities to react with other products to form char<ref name="ref1">[http://www.eagri.org/eagri50/AENG352/lec10.pdf Principles of Pyrolysis]</ref>. | ||
=== Fast === | |||
Fast pyrolysis provides conditions to maximise the production of the liquid fraction of the products that are bio-oils (e.g. pyrolysis oil and biocrude). The primary goal is producing a renewable fuel intermediate in the pathway to finished hydrocarbon fuels from [[Biomass|biomass]] feedstock<ref>[https://www.sciencedirect.com/science/article/pii/B9780128182130000011 Pyrolysis of Biomass for Fuels and Chemicals]</ref>. The typical fast pyrolysis conditions are: moderate pyrolysis treatment temperatures (600-1000°C), rapid heating rates of biomass particles (>100°C/min), combined with short residence times of the biomass particles and pyrolysis vapours (0.5-2s) at high temperatures. Combination of medium pyrolysis temperature with short vapour residence time ensures high yield of good quality pyrolysis liquids while keeping the char and gas yields to a minimum. Due to the low thermal conductivity of [[Biomass|biomass]], small particle sizes are required to achieve the high heating rate needed<ref>[https://www.sciencedirect.com/science/article/pii/B9780081004555000217 Handbook of Biofuels Production]</ref>. Fluidised bed reactors are best suited for this type of pyrolysis due to offering high heating rates, rapid devolatilization and are easy to operate<ref name="ref1" />. | Fast pyrolysis provides conditions to maximise the production of the liquid fraction of the products that are bio-oils (e.g. pyrolysis oil and biocrude). The primary goal is producing a renewable fuel intermediate in the pathway to finished hydrocarbon fuels from [[Biomass|biomass]] feedstock<ref>[https://www.sciencedirect.com/science/article/pii/B9780128182130000011 Pyrolysis of Biomass for Fuels and Chemicals]</ref>. The typical fast pyrolysis conditions are: moderate pyrolysis treatment temperatures (600-1000°C), rapid heating rates of biomass particles (>100°C/min), combined with short residence times of the biomass particles and pyrolysis vapours (0.5-2s) at high temperatures. Combination of medium pyrolysis temperature with short vapour residence time ensures high yield of good quality pyrolysis liquids while keeping the char and gas yields to a minimum. Due to the low thermal conductivity of [[Biomass|biomass]], small particle sizes are required to achieve the high heating rate needed<ref>[https://www.sciencedirect.com/science/article/pii/B9780081004555000217 Handbook of Biofuels Production]</ref>. Fluidised bed reactors are best suited for this type of pyrolysis due to offering high heating rates, rapid devolatilization and are easy to operate<ref name="ref1" />. | ||
=== Flash === | |||
Flash pyrolysis (sometimes referred to as very fast pyrolysis) is characterised by rapid heating rates (>1000°C/s) and high reaction temperatures (900-1300°C), producing high yields of bio-oil with low resulting water content and conversion efficiencies of up to 70%. The residence time is shorter than fast pyrolysis at less than 0.5 seconds. The [[Biomass|biomass]] feedstock must go through vigorous pre-treatment to reduce particle size as much as possible (around 105-250 μm) which is required to achieve such high heating and heat transfer rates<ref>[https://www.sciencedirect.com/science/article/pii/B9780444538789000096 New and Future Developments in Catalysis]</ref>. Entrained flow or fluidised bed reactors are considered the best pyrolyzers for this purpose<ref name="ref1" />. | Flash pyrolysis (sometimes referred to as very fast pyrolysis) is characterised by rapid heating rates (>1000°C/s) and high reaction temperatures (900-1300°C), producing high yields of bio-oil with low resulting water content and conversion efficiencies of up to 70%. The residence time is shorter than fast pyrolysis at less than 0.5 seconds. The [[Biomass|biomass]] feedstock must go through vigorous pre-treatment to reduce particle size as much as possible (around 105-250 μm) which is required to achieve such high heating and heat transfer rates<ref>[https://www.sciencedirect.com/science/article/pii/B9780444538789000096 New and Future Developments in Catalysis]</ref>. Entrained flow or fluidised bed reactors are considered the best pyrolyzers for this purpose<ref name="ref1" />. | ||
==References== | ==References== | ||
<references /> | <references /> |
Revision as of 15:04, 5 March 2021
Pyrolysis is the thermal degradation of waste in the absence of oxygen to produce gas (syngas), liquid and solid char fractions. The syngas is then generally burnt to raise steam and create electricity, but many plants are exploring the option of cleaning the syngas for use in a gas engine or separating the gas into usable fractions such as hydrogen for use, as an example, of liquid fuels which in turn may be eligible under the RTFO. The solid residue (sometimes described as a char) is a combination of non-combustible materials and carbon.
Description
The process generally requires an external heat source to maintain the temperature required and to avoid the introduction of air. There are a range of different types of approach, often aligned to the waste being processed, and include fixed bed reactors, batch or semi-batch reactors, rotary kilns, fluidized bed reactors, microwave assisted reactors and some innovative solutions like plasma or solar reactors [1].
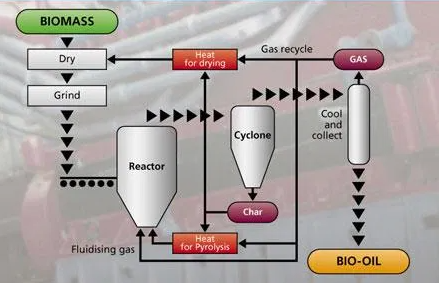
Typically, lower temperatures of between 300C to 850C are used during Pyrolysis of materials such as MSW. Pyrolysis processes tend to prefer consistent feedstocks and there is a limited track record of commercial scale Pyrolysis plant accepting MSW but a better track record of, for example, Pyrolysis of biomass [2].
Types of Pyrolysis
The pyrolysis process can be divided into three subcategories depending on the operating conditions: temperature, heating rate, particle size and solid residence time. The different types of pyrolysis are slow/conventional, fast and flash.
Slow/Conventional
Slow/conventional pyrolysis is a process where the heating rate is kept slow (around 0.1-1°C/s) which results in higher char yield than the liquid and gaseous products. This type of pyrolysis has been used for thousands of years for the production of charcoal. Biomass is heated to around 500°C in slow wood pyrolysis and the long vapour residence time in the reactor means the gas-phase products have ample opportunities to react with other products to form char[3].
Fast
Fast pyrolysis provides conditions to maximise the production of the liquid fraction of the products that are bio-oils (e.g. pyrolysis oil and biocrude). The primary goal is producing a renewable fuel intermediate in the pathway to finished hydrocarbon fuels from biomass feedstock[4]. The typical fast pyrolysis conditions are: moderate pyrolysis treatment temperatures (600-1000°C), rapid heating rates of biomass particles (>100°C/min), combined with short residence times of the biomass particles and pyrolysis vapours (0.5-2s) at high temperatures. Combination of medium pyrolysis temperature with short vapour residence time ensures high yield of good quality pyrolysis liquids while keeping the char and gas yields to a minimum. Due to the low thermal conductivity of biomass, small particle sizes are required to achieve the high heating rate needed[5]. Fluidised bed reactors are best suited for this type of pyrolysis due to offering high heating rates, rapid devolatilization and are easy to operate[3].
Flash
Flash pyrolysis (sometimes referred to as very fast pyrolysis) is characterised by rapid heating rates (>1000°C/s) and high reaction temperatures (900-1300°C), producing high yields of bio-oil with low resulting water content and conversion efficiencies of up to 70%. The residence time is shorter than fast pyrolysis at less than 0.5 seconds. The biomass feedstock must go through vigorous pre-treatment to reduce particle size as much as possible (around 105-250 μm) which is required to achieve such high heating and heat transfer rates[6]. Entrained flow or fluidised bed reactors are considered the best pyrolyzers for this purpose[3].
References
- ↑ Czajczyńska et al, 2017. Potential of pyrolysis processes in the waste management sector. Thermal Science and Engineering Progress, [online] 3, pp.171-197.
- ↑ Defra, 2013. Advanced Thermal Treatment of Municipal Solid Waste. London.
- ↑ 3.0 3.1 3.2 Principles of Pyrolysis
- ↑ Pyrolysis of Biomass for Fuels and Chemicals
- ↑ Handbook of Biofuels Production
- ↑ New and Future Developments in Catalysis