Pyrolysis: Difference between revisions
No edit summary |
No edit summary |
||
Line 20: | Line 20: | ||
[[File:Schematic diagram of a fixed bed pyrolysis reactor.png|250px|right|Schematic diagram of a fixed bed pyrolysis reactor. All rights reserved.]] | [[File:Schematic diagram of a fixed bed pyrolysis reactor.png|250px|right|Schematic diagram of a fixed bed pyrolysis reactor. All rights reserved.]] | ||
Fixed bed reactors were traditionally used to produce charcoal due to slow and poor heat transfer resulting in very low liquid charcoal yields. The technology is simple and reliable and utilises relatively uniform particle size. This type of gasifier is divided into downdraft and updraft. | Fixed bed reactors were traditionally used to produce charcoal due to slow and poor heat transfer resulting in very low liquid charcoal yields. The technology is simple and reliable and utilises relatively uniform particle size. This type of gasifier is divided into downdraft and updraft. | ||
In a downdraft fixed bed reactor, the solid moves slowly down a vertical shaft and reacts with the air introduced at the throat that supports the gasifying feedstock. The solid and product gas move downward in a co-current mode which produces a relatively clean gas with low tar and high carbon conversion rate. In an updraft fixed bed reactor, the feedstock also moves down a vertical shaft but in a counter-current mode. This results in a dirty product gas with high levels of tars which can be alleviated using tar crackers. However, due to the feedstock not moving during the process, it is difficult to obtain heating of large quantities of feedstock material on an industrial scale. This could be solved if the reactor used methods that enable better heat transfer such as heat pipes. | In a downdraft fixed bed reactor, the solid moves slowly down a vertical shaft and reacts with the air introduced at the throat that supports the gasifying [[Feedstock|feedstock]]. The solid and product gas move downward in a co-current mode which produces a relatively clean gas with low tar and high carbon conversion rate. In an updraft fixed bed reactor, the [[Feedstock|feedstock]] also moves down a vertical shaft but in a counter-current mode. This results in a dirty product gas with high levels of tars which can be alleviated using tar crackers. However, due to the [[Feedstock|feedstock]] not moving during the process, it is difficult to obtain heating of large quantities of [[Feedstock|feedstock]] material on an industrial scale. This could be solved if the reactor used methods that enable better heat transfer such as heat pipes. | ||
<ref>[https://www.sciencedirect.com/journal/thermal-science-and-engineering-progress/vol/3/suppl/C Potential of Pyrolysis Processes in the Waste Management Sector]</ref> | <ref>[https://www.sciencedirect.com/journal/thermal-science-and-engineering-progress/vol/3/suppl/C Potential of Pyrolysis Processes in the Waste Management Sector]</ref> | ||
<br clear=all /> | <br clear=all /> | ||
Line 27: | Line 28: | ||
==== Bubbling ==== | ==== Bubbling ==== | ||
[[File:Bubbling Fluidised Bed Reactor with an Electrostatic Precipitator.png|250px|right|Bubbling fluidised bed reactor with an electrostatic precipitator. All rights reserved.]] | [[File:Bubbling Fluidised Bed Reactor with an Electrostatic Precipitator.png|250px|right|Bubbling fluidised bed reactor with an electrostatic precipitator. All rights reserved.]] | ||
In bubbling fluidised beds, biomass particles are entered into a bed of hot sand fluidised by a recirculated product gas. The high heat transfer rates from the fluidised sand cause rapid heating of biomass particles and some ablation with the sand particles occurs. This type of reactor is characterised by good temperature control, limited turn down capacity and efficient heat transfer to biomass particles due to high solid density. <ref>[https://www.researchgate.net/publication/318678876_Review_of_Synthetic_Fuels_and_New_Materials_Production_Based_on_Pyrolysis_Technologies Review of Synthetic Fuels and New Materials Production Based on Pyrolysis Technologies]</ref> | In bubbling fluidised beds, biomass particles are entered into a bed of hot sand fluidised by a recirculated product gas. The high heat transfer rates from the fluidised sand cause rapid heating of [[Biomass|biomass]] particles and some ablation with the sand particles occurs. This type of reactor is characterised by good temperature control, limited turn down capacity and efficient heat transfer to [[Biomass|biomass]] particles due to high solid density. | ||
<ref>[https://www.researchgate.net/publication/318678876_Review_of_Synthetic_Fuels_and_New_Materials_Production_Based_on_Pyrolysis_Technologies Review of Synthetic Fuels and New Materials Production Based on Pyrolysis Technologies]</ref> | |||
<br clear=all /> | <br clear=all /> | ||
==== Circulating ==== | ==== Circulating ==== | ||
[[File:Circulating Fluidised Bed Reactor.png|250px|right|Circulating fluidised bed reactor. All rights reserved.]] | [[File:Circulating Fluidised Bed Reactor.png|250px|right|Circulating fluidised bed reactor. All rights reserved.]] | ||
In circulating fluidised beds, biomass particles are introduced into a circulating bed of hot sand. The recirculated product gas, sand and biomass move together in the reactor. The high heat transfer rates from the sand ensure rapid heating of the biomass and ablation is more prevalent than bubbling fluidised beds. This reactor is characterised by good temperature control and high heating rates. The residence time for the tar produced is around the same for the vapour and gas and can be separated by cyclone. | In circulating fluidised beds, [[Biomass|biomass]] particles are introduced into a circulating bed of hot sand. The recirculated product gas, sand and [[Biomass|biomass]] move together in the reactor. The high heat transfer rates from the sand ensure rapid heating of the [[Biomass|biomass]] and ablation is more prevalent than bubbling fluidised beds. This reactor is characterised by good temperature control and high heating rates. The residence time for the tar produced is around the same for the vapour and gas and can be separated by cyclone. | ||
<ref name="ref2">[https://www.researchgate.net/publication/330335978_Design_of_A_Fluidized_Bed_Reactor_For_Biomass_Pyrolysis Design of A Fluidized Bed Reactor For Biomass Pyrolysis]</ref> | <ref name="ref2">[https://www.researchgate.net/publication/330335978_Design_of_A_Fluidized_Bed_Reactor_For_Biomass_Pyrolysis Design of A Fluidized Bed Reactor For Biomass Pyrolysis]</ref> | ||
<br clear=all /> | <br clear=all /> | ||
=== Vacuum Furnace Reactor === | === Vacuum Furnace Reactor === | ||
[[File:Schematic for a Vacuum Pyrolysis Reactor.png|250px|right|Schematic for a vacuum pyrolysis reactor. All rights reserved.]] | [[File:Schematic for a Vacuum Pyrolysis Reactor.png|250px|right|Schematic for a vacuum pyrolysis reactor. All rights reserved.]] | ||
For a vacuum furnace reactor, the biomass is thermally decomposed under reduced pressure. This produces vapours which are quickly removed from the vacuum and recovered as bio-oil via condensation. This reactor has the ability to produce larger particles than most fast pyrolysis reactors and there is less tar in the bio-oil product due to lower gas velocities. The typical liquid yields for dry biomass feed produced from vacuum furnace reactors range from 35% to 50%. | For a vacuum furnace reactor, the [[Biomass|biomass]] is thermally decomposed under reduced pressure. This produces vapours which are quickly removed from the vacuum and recovered as bio-oil via condensation. This reactor has the ability to produce larger particles than most fast pyrolysis reactors and there is less tar in the bio-oil product due to lower gas velocities. The typical liquid yields for dry [[Biomass|biomass]] feed produced from vacuum furnace reactors range from 35% to 50%. | ||
<ref>[https://www.researchgate.net/publication/333827218_Liquefaction_of_Biomass_and_Upgrading_of_Bio-Oil_A_Review Liquefaction of Biomass and Upgrading of Bio-Oil]</ref> | <ref>[https://www.researchgate.net/publication/333827218_Liquefaction_of_Biomass_and_Upgrading_of_Bio-Oil_A_Review Liquefaction of Biomass and Upgrading of Bio-Oil]</ref> | ||
<br clear=all /> | <br clear=all /> | ||
Line 42: | Line 47: | ||
[[File:Ablative Pyrolyser.png|250px|right|Ablative pyrolysis reactor. All rights reserved.]] | [[File:Ablative Pyrolyser.png|250px|right|Ablative pyrolysis reactor. All rights reserved.]] | ||
The ablative reactor provides high relative motion between the reactor wall and the particles in the presence of high pressure exerted by the particles of the hot reactor wall. The system is intensive and the process is mechanically driven so the reactor is complex. This type of reactor has advantages over fluidised bed: | The ablative reactor provides high relative motion between the reactor wall and the particles in the presence of high pressure exerted by the particles of the hot reactor wall. The system is intensive and the process is mechanically driven so the reactor is complex. This type of reactor has advantages over fluidised bed: | ||
*No pre-treatment/sorting of the biomass is required because it is in direct contact with the hot surface so is not influenced by particle size | *No pre-treatment/sorting of the [[Biomass|biomass]] is required because it is in direct contact with the hot surface so is not influenced by particle size | ||
*They have good heat transfer with high heating rates and relatively small contact surface because their compact design | *They have good heat transfer with high heating rates and relatively small contact surface because their compact design | ||
*They have high energy and cost efficiency as no heating and cooling of fluidizing gases is required | *They have high energy and cost efficiency as no heating and cooling of fluidizing gases is required | ||
*They allow installation of condensation units with a small volume, requiring less space at lower costs | *They allow installation of condensation units with a small volume, requiring less space at lower costs | ||
<ref name="ref2" /> | <ref name="ref2" /> | ||
<br clear=all /> | <br clear=all /> | ||
=== Rotating Cone Reactor === | === Rotating Cone Reactor === | ||
[[File:Rotating Cone Pyrolysis Reactor.png|250px|right|Rotating cone pyrolysis reactor. All rights reserved.]] | [[File:Rotating Cone Pyrolysis Reactor.png|250px|right|Rotating cone pyrolysis reactor. All rights reserved.]] | ||
The rotating cone reactor is a novel type for flash pyrolysis. It is characterised by rapid heating, a short residence time for solids and negligible char formation. Biomass materials (wood, rice husks, olive stones) are pulverised and fed into the rotating cone pyrolyzer. There is also a riser for sand recycling and a bubbling char combustor for char burn off in which carrier gas is required. Relatively fine particles are needed to produce good liquid yields of 60% to 70% of dry feed. However, this type of reactor is still at pilot scale as there is no commercial applications as of yet. | The rotating cone reactor is a novel type for flash pyrolysis. It is characterised by rapid heating, a short residence time for solids and negligible char formation. [[Biomass]] materials ([[Wood|wood]], rice husks, olive stones) are pulverised and fed into the rotating cone pyrolyzer. There is also a riser for sand recycling and a bubbling char combustor for char burn off in which carrier gas is required. Relatively fine particles are needed to produce good liquid yields of 60% to 70% of dry feed. However, this type of reactor is still at pilot scale as there is no commercial applications as of yet. | ||
<ref name="ref2" /> | <ref name="ref2" /> | ||
<br clear=all /> | <br clear=all /> | ||
=== Auger Reactor === | === Auger Reactor === | ||
[[File:Diagram of an auger pyrolysis reactor.png|250px|right|Diagram of an auger pyrolysis reactor. All rights reserved.]] | [[File:Diagram of an auger pyrolysis reactor.png|250px|right|Diagram of an auger pyrolysis reactor. All rights reserved.]] | ||
In an auger reactor, hot sand and biomass particles enter at one end of a screw. The screw mixes these inputs and conveys them along, providing good control of the biomass residence time. The process does not dilute the pyrolysis products with the carrier or fluidising gas, but the sand must be reheated in a separate vessel. Mechanical reliability is a concern and so there is currently no large-scale implementation of this reactor type. Advantages of this reactor: | In an auger reactor, hot sand and [[Biomass|biomass]] particles enter at one end of a screw. The screw mixes these inputs and conveys them along, providing good control of the [[Biomass|biomass]] residence time. The process does not dilute the pyrolysis products with the carrier or fluidising gas, but the sand must be reheated in a separate vessel. Mechanical reliability is a concern and so there is currently no large-scale implementation of this reactor type. Advantages of this reactor: | ||
*Compact size | *Compact size | ||
*No carrier gas required | *No carrier gas required |
Revision as of 11:12, 8 March 2021
Pyrolysis is the thermal degradation of waste in the absence of oxygen to produce gas (syngas), liquid and solid char fractions. The syngas is then generally burnt to raise steam and create electricity, but many plants are exploring the option of cleaning the syngas for use in a gas engine or separating the gas into usable fractions such as hydrogen for use, as an example, of liquid fuels which in turn may be eligible under the RTFO. The solid residue (sometimes described as a char) is a combination of non-combustible materials and carbon.
Description
The process generally requires an external heat source to maintain the temperature required and to avoid the introduction of air. There are a range of different types of approach, often aligned to the waste being processed, and include fixed bed reactors, batch or semi-batch reactors, rotary kilns, fluidized bed reactors, microwave assisted reactors and some innovative solutions like plasma or solar reactors [1].
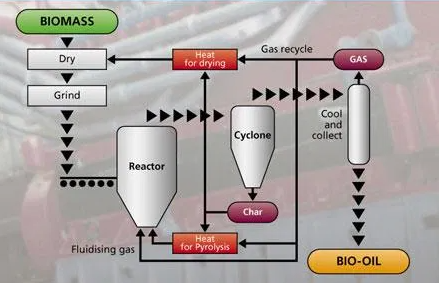
Typically, lower temperatures of between 300C to 850C are used during Pyrolysis of materials such as MSW. Pyrolysis processes tend to prefer consistent feedstocks and there is a limited track record of commercial scale Pyrolysis plant accepting MSW but a better track record of, for example, Pyrolysis of biomass [2].
Types of Pyrolysis
The pyrolysis process can be divided into three subcategories depending on the operating conditions: temperature, heating rate, particle size and solid residence time. The different types of pyrolysis are slow/conventional, fast and flash.
Slow/Conventional
Slow/conventional pyrolysis is a process where the heating rate is kept slow (around 0.1-1°C/s) which results in higher char yield than the liquid and gaseous products. This type of pyrolysis has been used for thousands of years for the production of charcoal. Biomass is heated to around 500°C in slow wood pyrolysis and the long vapour residence time in the reactor means the gas-phase products have ample opportunities to react with other products to form char[3].
Fast
Fast pyrolysis provides conditions to maximise the production of the liquid fraction of the products that are bio-oils (e.g. pyrolysis oil and biocrude). The primary goal is producing a renewable fuel intermediate in the pathway to finished hydrocarbon fuels from biomass feedstock[4]. The typical fast pyrolysis conditions are: moderate pyrolysis treatment temperatures (600-1000°C), rapid heating rates of biomass particles (>100°C/min), combined with short residence times of the biomass particles and pyrolysis vapours (0.5-2s) at high temperatures. Combination of medium pyrolysis temperature with short vapour residence time ensures high yield of good quality pyrolysis liquids while keeping the char and gas yields to a minimum. Due to the low thermal conductivity of biomass, small particle sizes are required to achieve the high heating rate needed[5]. Fluidised bed reactors are best suited for this type of pyrolysis due to offering high heating rates, rapid devolatilization and are easy to operate[3].
Flash
Flash pyrolysis (sometimes referred to as very fast pyrolysis) is characterised by rapid heating rates (>1000°C/s) and high reaction temperatures (900-1300°C), producing high yields of bio-oil with low resulting water content and conversion efficiencies of up to 70%. The residence time is shorter than fast pyrolysis at less than 0.5 seconds. The biomass feedstock must go through vigorous pre-treatment to reduce particle size as much as possible (around 105-250 μm) which is required to achieve such high heating and heat transfer rates[6]. Entrained flow or fluidised bed reactors are considered the best pyrolyzers for this purpose[3].
Pyrolysis Reactors
Fixed Bed Reactor
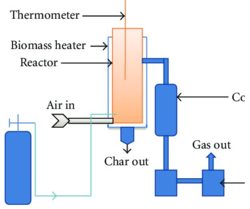
Fixed bed reactors were traditionally used to produce charcoal due to slow and poor heat transfer resulting in very low liquid charcoal yields. The technology is simple and reliable and utilises relatively uniform particle size. This type of gasifier is divided into downdraft and updraft. In a downdraft fixed bed reactor, the solid moves slowly down a vertical shaft and reacts with the air introduced at the throat that supports the gasifying feedstock. The solid and product gas move downward in a co-current mode which produces a relatively clean gas with low tar and high carbon conversion rate. In an updraft fixed bed reactor, the feedstock also moves down a vertical shaft but in a counter-current mode. This results in a dirty product gas with high levels of tars which can be alleviated using tar crackers. However, due to the feedstock not moving during the process, it is difficult to obtain heating of large quantities of feedstock material on an industrial scale. This could be solved if the reactor used methods that enable better heat transfer such as heat pipes.
Fluidised Bed Reactor
Fluidised bed reactors are typically used for fast pyrolysis and are characterised by a high heating rate and small particle size. This type of reactor can be split into bubbling and circulating fluidised bed.
Bubbling
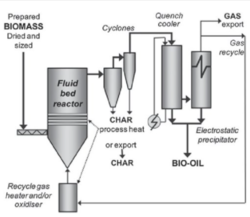
In bubbling fluidised beds, biomass particles are entered into a bed of hot sand fluidised by a recirculated product gas. The high heat transfer rates from the fluidised sand cause rapid heating of biomass particles and some ablation with the sand particles occurs. This type of reactor is characterised by good temperature control, limited turn down capacity and efficient heat transfer to biomass particles due to high solid density.
Circulating
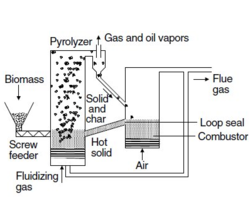
In circulating fluidised beds, biomass particles are introduced into a circulating bed of hot sand. The recirculated product gas, sand and biomass move together in the reactor. The high heat transfer rates from the sand ensure rapid heating of the biomass and ablation is more prevalent than bubbling fluidised beds. This reactor is characterised by good temperature control and high heating rates. The residence time for the tar produced is around the same for the vapour and gas and can be separated by cyclone.
Vacuum Furnace Reactor

For a vacuum furnace reactor, the biomass is thermally decomposed under reduced pressure. This produces vapours which are quickly removed from the vacuum and recovered as bio-oil via condensation. This reactor has the ability to produce larger particles than most fast pyrolysis reactors and there is less tar in the bio-oil product due to lower gas velocities. The typical liquid yields for dry biomass feed produced from vacuum furnace reactors range from 35% to 50%.
Ablative Reactor
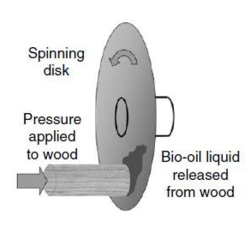
The ablative reactor provides high relative motion between the reactor wall and the particles in the presence of high pressure exerted by the particles of the hot reactor wall. The system is intensive and the process is mechanically driven so the reactor is complex. This type of reactor has advantages over fluidised bed:
- No pre-treatment/sorting of the biomass is required because it is in direct contact with the hot surface so is not influenced by particle size
- They have good heat transfer with high heating rates and relatively small contact surface because their compact design
- They have high energy and cost efficiency as no heating and cooling of fluidizing gases is required
- They allow installation of condensation units with a small volume, requiring less space at lower costs
Rotating Cone Reactor
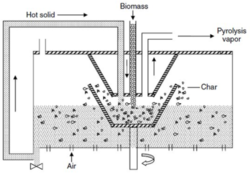
The rotating cone reactor is a novel type for flash pyrolysis. It is characterised by rapid heating, a short residence time for solids and negligible char formation. Biomass materials (wood, rice husks, olive stones) are pulverised and fed into the rotating cone pyrolyzer. There is also a riser for sand recycling and a bubbling char combustor for char burn off in which carrier gas is required. Relatively fine particles are needed to produce good liquid yields of 60% to 70% of dry feed. However, this type of reactor is still at pilot scale as there is no commercial applications as of yet.
Auger Reactor
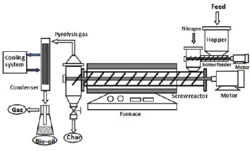
In an auger reactor, hot sand and biomass particles enter at one end of a screw. The screw mixes these inputs and conveys them along, providing good control of the biomass residence time. The process does not dilute the pyrolysis products with the carrier or fluidising gas, but the sand must be reheated in a separate vessel. Mechanical reliability is a concern and so there is currently no large-scale implementation of this reactor type. Advantages of this reactor:
- Compact size
- No carrier gas required
- Lower operating temperature (400°C) [3]
References
- ↑ Czajczyńska et al, 2017. Potential of pyrolysis processes in the waste management sector. Thermal Science and Engineering Progress, [online] 3, pp.171-197.
- ↑ Defra, 2013. Advanced Thermal Treatment of Municipal Solid Waste. London.
- ↑ 3.0 3.1 3.2 3.3 Principles of Pyrolysis
- ↑ Pyrolysis of Biomass for Fuels and Chemicals
- ↑ Handbook of Biofuels Production
- ↑ New and Future Developments in Catalysis
- ↑ Potential of Pyrolysis Processes in the Waste Management Sector
- ↑ Review of Synthetic Fuels and New Materials Production Based on Pyrolysis Technologies
- ↑ 9.0 9.1 9.2 Design of A Fluidized Bed Reactor For Biomass Pyrolysis
- ↑ Liquefaction of Biomass and Upgrading of Bio-Oil
- ↑ Effect of Temperature on Product Yield from the Pyrolysis of Soybean Cake in an Auger Reactor