Magnetic Separator
A Magnetic Separator is a machine that is used to separate and recover ferrous, magnetic metals such as iron and steel from the non-magnetic fraction in the waste stream. This is achieved by passing waste materials, via a conveyor, over or under strong magnets.
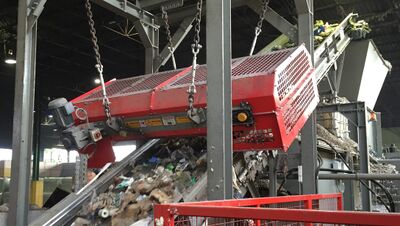
Overview
A Magnetic Separator separates out the ferrous portion of the waste stream from the non-ferrous. The separation process extracts strongly magnetic (ferromagnetic) and even weekly magnetic (paramagnetic) materials by passing the waste stream over (or under) powerful magnets[1]. The conventional use of magnetic separation can be placed into two categories: the purification of feeds with magnetic components (with the desired product being non-magnetic) and the concentration of magnetic materials (with the desired product being magnetic)[2]. Close control of the speed of passage through the magnetic field is essential for efficient sorting/recovery rates[3].
Applications[4]
- Waste management applications - to remove the ferrous portion from different waste materials such as:
- Dry Recyclables/DMR (mixed and twin streams)
- MSW
- C&I Waste
- C&D Waste/Skip Waste
- Waste Derived Fuel - to ensure reduction of metal in RDF and SRF to meet end specification
- Scrap Metal Separation - to remove ferrous from mixed metal streams
- Fridge Recycling Plants- to remove ferrous from mixed metal, plastic and glass stream
- Tyres Recycling- to remove ferrous from rubber stream
- Incinerator Bottom Ash - to remove ferrous from ash as part of production of IBAA
- Biomass - to remove ferrous from Wood Waste to ensure purity for onward use
- WEEE Processing - to remove ferrous from mixed metal and plastic streams
- Window Frame Recycling - to remove ferrous from plastic streams
Benefits
- Large capacity
- High efficiency
- Continuous process
- Low operating cost[5]
The Process
There are two primary types of Magnetic Separator:
- Overband Magnets (which include electromagnetic overband magnets) - where the waste is passed under a magnet and a rotating conveyor belt pulls the ferrous metal away from the transporting conveyor. There are two types of configuration for overband magnets
- Inline Overband Magnets - where the magnet and extracting conveyor are aligned with the transporting conveyor
- Crossbelt Overband Magnets - where the magnet is at right angles to the transporting conveyor
- Drum Magnets where the waste is passed over a rotating magnet to pull the ferrous metal away from the transporting conveyor belt
Overband Magnet
Schematic Diagram of a Crossbelt Magnetic Separator[4] |
1. The feed material is fed onto the conveyor belt and is transported under the magnet. |
|
2. The ferrous material is drawn up towards the magnet from the waste stream. | ||
3. A rotating conveyor with paddles carries the ferrous material over the side of the transporting conveyor where it drops out of the magnetic field into a separate bin. | ||
4. The non-magnetic material continues on the transporting conveyor unaffected by the process. |
Drum Magnet
Schematic Diagram of a Drum Magnetic Separator[1] |
1. The feed material is fed onto the conveyor belt and is transported towards the magnetic pulley end. |
|
2. The waste stream falls off the end of the pulley and travels downward by the combined action of gravitational and frictional forces. | ||
3. Magnetic forces produced by the stationary magnets within the pulley hold the ferrous material against the rotating drum and deposit them in the ferromagnetic bin. | ||
4. The diamagnetic (non-magnetic) material falls into a separate bin as they are repelled from the magnetic field[1]. |